Technology Description
PROFINET is the standard for industrial networking in automation. It connects devices, systems, and cells, facilitating faster, safer, less costly and higher quality manufacturing. It easily integrates existing systems and equipment while bringing the richness of Ethernet down to the factory floor.
Do you want to learn what PROFINET is and how it works? This short video covers a comprehensive overview of PROFINET. It includes details on the protocol mechanisms, installation, configuration, network components, and more. PROFINET growth continues to accelerate year over year across all industry verticals.
Learn More about the Technology
PROFINET, derived from "PROcess FIeld NETwork," is widely regarded as the most advanced Industrial Ethernet solution globally. This communication protocol serves as a vital tool within the automation industry, facilitating real-time data exchange between controllers and devices. Controllers, including PLCs, DCSs, or PACs, can communicate with various devices such as I/O blocks, vision systems, RFID readers, drives, process instruments, proxies, or even other controllers. While PROFINET fully leverages the features of office Ethernet, there are notable distinctions. Office Ethernet lacks the capability for real-time performance required in industrial automation and is less resilient in harsh industrial environments.
Drawing from the success of PROFIBUS, the leading fieldbus in automation networking, PI Working Groups, consisting of over 500 experts from major automation suppliers, dedicated years of effort to develop PROFINET. This comprehensive real-time Ethernet solution for automation operates effectively in challenging industrial environments, delivering the speed and precision demanded by manufacturing plants. Moreover, PROFINET offers additional functionalities like Safety, Energy Management, and IT Integration, which can be utilized in conjunction with control and monitoring functions, allowing users the freedom to choose the services that suit their needs.
Here are several advantages of employing PROFINET at the IO level:
- Ethernet-based Communication: PROFINET is built upon standard Ethernet technology, enabling high-speed data transmission, flexibility, and compatibility with existing IT infrastructure.
- Real-Time Communication: PROFINET supports real-time communication, ensuring precise and deterministic control in industrial automation applications. It guarantees reliable transmission of time-critical data with low latency.
- Highly Scalable Architectures: PROFINET offers a scalable architecture that facilitates easy system expansion or modification to meet specific requirements. It supports various network topologies such as line, ring, and star, providing flexibility in system design.
PROFINET effectively addresses the requirements of IT and plant floor automation through its three communication channels:
- Standard TCP/IP: This channel is suitable for non-deterministic functions such as parametrization, video/audio transmissions, and data transfer to higher level IT systems.
- Real Time (PROFINET RT): By bypassing TCP/IP layers, this channel ensures deterministic performance for automation applications in the 1-10 ms range. It provides a software-based solution that is well-suited for typical I/O applications, including motion control and high-performance requirements.
- Isochronous Real Time (PROFINET IRT): Through signal prioritization and scheduled switching, this channel delivers highly precise synchronization, particularly for motion control applications. It supports cycle rates in the sub-millisecond range, with minimal jitter in the microsecond range. Hardware support in the form of readily-available ASICs is necessary for this service.
- TSN (Time Sensitive Networking): Currently being developed on the basis of use cases using the relevant IEEE Ethernet standards.
All communication channels can be used simultaneously. Bandwidth sharing guarantees that at least 50% of every I/O cycle remains available for TCP/IP communications. When combined with ruggedized cabling, connectors, and Ethernet switches, PROFINET can meet the diverse needs of automation. You can find more information about PROFINET's advanced features, positioning it as the world's most advanced Industrial Ethernet, in the link provided.
It's important to note that PROFINET fully complies with internationally-accepted Ethernet standards. In contrast, certain Industrial Ethernets deviate from Ethernet conventions and lack compatibility with office-based systems. Consequently, such non-compliant networks face challenges in interoperability within enterprise architectures and alongside fully compliant Industrial Ethernets.
As the adoption of fieldbus technology increased, users recognized the growing significance of tighter integration with IT systems. While fieldbus systems could be incorporated into plant networking hierarchies through the use of gateways and other devices, this approach often proved cumbersome and costly. Consequently, users began to question whether office networking technologies, particularly Ethernet, could be extended to the factory floor. The ultimate goal, they argued, was for automation systems themselves to be based on Ethernet.
In reality, Ethernet has been utilized on the factory floor for almost as long as it has been employed in office settings, albeit primarily for inter-cell communications rather than IO (input/output). However, the implementation of Ethernet has lacked standardization, with installations typically relying on proprietary solutions. Furthermore, there have been practical challenges associated with this approach, including:
- Inadequate real-time performance of office Ethernet for industrial IO.
- Insufficient precision determinism of office Ethernet for advanced motion control.
- Inability of office Ethernet to withstand the physical conditions commonly encountered in manufacturing environments (such as dust, heat, humidity, corrosion, and electromagnetic interference).
- Fortunately, these challenges can be overcome, leading to the development of what is now referred to as 'Industrial Ethernet'.
PROFINET stands out as it is fully compatible with standard office Ethernet, allowing it to coexist and operate seamlessly on a single network cable alongside other Industrial Ethernet technologies, such as OPC UA. This coexistence implies that these Industrial Ethernets can share the same network infrastructure.
However, it is crucial to note that coexistence does not imply interoperability between different systems. Due to protocol differences, Industrial Ethernets cannot directly communicate with each other unless additional hardware, such as protocol converters, is utilized.
Furthermore, it is important to acknowledge that some Industrial Ethernet technologies deviate from the international Ethernet standard. These non-standard Industrial Ethernets require deployment on closed networks, although they may not necessarily be proprietary. From an Ethernet perspective, these non-standard Industrial Ethernets do not conform to the recognized standard.
PROFINET was developed through the collaborative efforts of PI Working Groups, which involved over 500 engineers from prominent automation vendors. Leveraging their extensive field experience with PROFIBUS as a foundation, the engineers selectively incorporated Ethernet's specific attributes to cater to the unique requirements of automation.
PROFINET offers a comprehensive range of specialized features that complement existing communication capabilities. These features are designed to simplify the work of designers, engineers, maintenance personnel, and managers in various automation applications. It is not necessary to utilize all features simultaneously; instead, users can select the specific features that align with their particular circumstances.
Here are some notable features:
- Configuration in run: Allows device configuration and setup even when the controller is in operation.
- Shared device: Facilitates the distribution of device functions among multiple controllers.
- Application profiles: Includes safety, energy management, motion control, and other profiles tailored for specific applications.
- Redundancy: Offers options for device, controller, media, and network redundancy.
- Simple device replacement: Automatically assigns a name to a replaced IO device in case of device failure and replacement.
- Tool calling interface: Allows the invocation of device-specific engineering tools.
- And many more…
Conceptually, PROFINET can be seen as a modular solution that provides flexibility. Users can start with a simple configuration and gradually incorporate additional functionality as needed.
PROFINET follows a similar approach to PROFIBUS when it comes to handling I/O. An engineering tool is associated with the controller, which retrieves information about the IO Devices from a GSD file (General Station Description). Once the project is configured in the software, it is downloaded to the controller, enabling communication with the I/O Devices.
The I/O Devices are structured in a hierarchical manner, comprising Device, Module, and Channel. Inputs and Outputs are exchanged between the controller and I/O Devices in a cyclic manner, meaning they occur regularly within a defined update cycle time set by the controller. This cyclic data exchange facilitates real-time control and monitoring of the process.
In addition to cyclic data, there is also the transmission of acyclic data. Acyclic data includes information such as diagnostic data, which is not required as frequently as the cyclic data. This data is communicated as needed and does not adhere to a fixed cyclic update cycle.
Overall, PROFINET employs a familiar approach to I/O management, ensuring efficient and reliable communication between the controller and I/O Devices, enabling seamless control and monitoring of industrial processes.
PROFINET incorporates wireless technology as part of its specification, utilizing well-established wireless standards such as 5G, Wi-Fi, and Bluetooth. The inclusion of standardized wireless technology provides the advantage of unrestricted connectivity compared to traditional cabling methods. Additionally, PI (PROFIBUS & PROFINET International) actively contributes to the standardization of wireless networking solutions specifically designed for industrial applications in both Process Automation and Factory Automation domains.
In Process Automation, PI is a key advocate for the WirelessHART protocol (ISA 100.11a). In collaboration with other process automation organizations, including HART Communication Foundation and Fieldbus Foundation, PI has established a standard adapter interface for WirelessHART. This collaboration ensures that users can benefit from a unified technology offering from multiple vendors, streamlining compatibility and integration.
In Discrete Automation, Factory Automation presents distinct requirements compared to Process Automation. Bandwidth demands are typically higher, and network resilience, security, and redundancy are critical factors. Similar to enterprise environments, factory settings already employ 5G, Wi-Fi, and Bluetooth solutions. Additionally, PI Working Groups are currently developing a set of standards for sensor/actuator communications in conjunction with PROFIBUS and PROFINET. Bluetooth has been selected as the communication medium, complemented by IO-Link as the interface for end devices.
By incorporating wireless technologies into PROFINET, PI aims to enhance connectivity options and address the diverse needs of both Process Automation and Factory Automation, ensuring efficient and reliable communication in industrial environments.
The openness of Ethernet allows for convenient access to networks from anywhere in the world using commonly available tools like web browsers. While this presents significant advantages, it also raises concerns about network security across the enterprise.
PROFINET addresses these critical security issues through various means, as defined in a dedicated security specification:
- Guarding against errors and improper operation: PROFINET incorporates mechanisms to detect and prevent errors or improper operations that could compromise the network's integrity or disrupt its functioning.
- Preventing unauthorized access: PROFINET employs measures to prevent unauthorized access to the network, which could potentially lead to network manipulation or espionage. Access controls, authentication protocols, and encryption methods are implemented to ensure that only authorized personnel can access the network.
- Utilizing proven and certified security standards: PROFINET leverages established and certified security standards, such as firewalls and virtual private networks (VPNs), to enhance network security. These standards provide robust protection against external threats and help safeguard the integrity of the control network.
By implementing these security measures, a PROFINET control network can be fully protected, ensuring the integrity and confidentiality of data, while still allowing authorized personnel to access and manage the network as needed. The aim is to strike a balance between robust security measures and providing necessary access for authorized personnel without imposing unnecessary restrictions.
PROFINET provides an exceptional level of diagnostic capability, enabling both local and remote diagnostics using standardized displays. Diagnostic overviews offer varying levels of detail to cater to specific needs, showcasing device, module, channel, and interrupt activity. Current fault events can be acknowledged, and PROFINET's Identification and Maintenance (I&M) functions are seamlessly facilitated. Clear and understandable naming conventions eliminate the need to search for obscure tag names or numbers before addressing the issue. Additionally, PROFINET allows for topology layouts that visually depict the network structure of your plant.
For instance, a diagnostics web interface can be accessed through integrated web servers embedded in automation devices. This means that a standard Internet browser can be utilized to access diagnostic displays. Engineers no longer need to be physically present on-site to diagnose faults, as access to plant networks can be easily facilitated over an intranet or even the internet. Automated, event-driven messages can be sent to engineering staff through SMS or email, ensuring prompt notification of critical events.
Cable diagnostics are equally straightforward with standardized displays that provide accurate topology views of the network, facilitating rapid fault localization. Standard Ethernet tools like SNMP (Simple Network Management Protocol) and Ethereal can be employed for diagnostics. Furthermore, easy access to vendor-specific tools is available for more complex devices, ensuring comprehensive diagnostic capabilities.
Overall, PROFINET empowers users with extensive diagnostic features, offering convenience, remote accessibility, and comprehensive insights into the network and device status for efficient troubleshooting and maintenance.
PROFINET demonstrates full compatibility with standard Ethernet, enabling it to deliver classic TCP/IP performance when necessary. This capability allows for seamless scalability to meet the requirements of manufacturing facilities of varying sizes. Moreover, PROFINET networks can easily integrate with existing Ethernet networks, including higher-level enterprise systems such as MES (Manufacturing Execution Systems) and ERP (Enterprise Resource Planning). This integration facilitates data exchange and communication between production systems and business systems, optimizing overall operational efficiency.
Regarding the OPC Unified Architecture (UA), the OPC UA PROFINET Companion Specification facilitates the use of standard OPC UA Services to interact with PROFINET device objects in a manner that is not tied to a specific vendor. This interaction can be established either through an integrated OPC UA Server within the PROFINET device itself or via an OPC UA Server that consolidates Object Dictionaries from multiple PROFINET devices. This capability enables horizontal communication between PROFINET devices and OPC UA devices, as well as vertical communication originating from devices at the process or enterprise level. This vertical communication can be employed for various purposes, such as diagnostics, configuration, condition monitoring, visualization, and more.
Specifically, this facilitates communication with devices like operator stations via the controller level and the transmission of production data from devices to corporate IT systems, especially in scenarios involving different providers. OPC UA serves as the bridge for non-deterministic communication between various types of devices at this level and across different levels. PROFINET, on the other hand, handles the transmission of deterministic real-time data and control-related acyclic data within automation systems. Together, PROFINET and OPC UA seamlessly complement each other, as PROFINET enables open communication over TCP/IP in parallel without incurring additional costs.
Within reasonable boundaries and while adhering to established security and management strategies, PROFINET has the potential to extend its reach across the enterprise. By leveraging PROFINET, production data can be accessed in real time by supervisory staff from virtually any location within the enterprise. This enhanced visibility and accessibility enable better management of plant operations, skills utilization, and asset utilization. Furthermore, real-time production data empowers improved production scheduling and streamlined order processing.
Additionally, PROFINET can provide full Internet connectivity, enabling global enterprises to operate more efficiently across multiple locations worldwide. This capability enhances collaboration, data sharing, and coordination, promoting consistent and optimized operations throughout the organization.
In summary, PROFINET's compatibility with standard Ethernet, seamless integration with enterprise systems, real-time data availability, and Internet connectivity contribute to enhanced management, improved production processes, and increased operational efficiency at both local and global scales.
PROFIdrive is a vendor-neutral application profile developed by PROFIBUS and PROFINET International (PI). Its primary focus lies in the realm of drives, encoders, motors, and their versatile applications, spanning from simple to highly demanding motion control tasks. PROFIdrive serves as the cornerstone for defining device behavior and techniques for accessing internal device data for electric drives connected to both PROFINET and PROFIBUS networks. This spectrum encompasses basic frequency converters to high-performance servo controllers.
One of PROFIdrive's key strengths is its commitment to interoperability. It achieves this through standardized drive IO data sets, messages, and parameter sets, while also allowing manufacturers to incorporate proprietary features, fostering healthy competition and innovation.
This profile delves deep into the practical application of communication functions, encompassing device-to-device communication, equidistance, and clock cycle synchronization (isochronous mode) within drive applications. Furthermore, it meticulously specifies all device characteristics that impact interfaces connected to controllers via PROFINET or PROFIBUS. This encompasses elements such as the state machine (sequence control), encoder interfaces, value scaling, standard telegrams, and access to drive parameters.
PROFIdrive accommodates both central and distributed motion control concepts, offering flexibility in automation solutions. It's specified by PROFIBUS and PROFINET International (PI) as a future-proof standard, compliant with IEC 61800-7. In addition, PROFIdrive can be seamlessly integrated with other application profiles like PROFIsafe and PROFIenergy, enhancing drive capabilities within modern automation projects.
To keep the drive interface as simple as possible and free from technology functions, PROFIdrive minimizes the influence of referencing models and the functionality and performance of the PROFINET/PROFIBUS master on the drive interface.
Given the diverse landscape of drive applications, PROFIdrive classifies them into six application classes, addressing a wide spectrum of scenarios:
Class 1 – Standard drives (e.g., pumps, fans, agitators).
Class 2 – Standard drives with technological functions.
Class 3 – Positioning drives.
Class 4 – Motion control drives with central, higher-level motion control intelligence and the innovative "Dynamic Servo Control" positioning concept.
Class 5 – Motion control drives with central, higher-level motion control intelligence and position setpoint interface.
Class 6 – Motion control drives with distributed motion control intelligence integrated into the drives.
This classification empowers users to tailor PROFIdrive to their specific drive application needs, making it a versatile and adaptable solution.
More Information on PROFIdrive
Safety systems play a crucial role in protecting equipment, individuals, and the environment. Traditional safety systems relied on separate wired circuits, which were costly to build, commission, and maintain. However, with advancements in technology, functional safety can now be achieved over the bus, shifting from safety in hard relays to safety in logic. By adding functional safety to an existing automation network, significant engineering effort can be reduced, cabling requirements are minimized, commissioning time is accelerated, and maintenance becomes easier. Networked safety systems offer enhanced flexibility, allowing for easy zoning, partitioning, and modification of safety strategies. Furthermore, innovative safety architectures are made possible with the emergence of new generations of safety devices like laser scanners.
PROFIsafe is an additional software layer that enables functional safety over the bus, operating on top of existing PROFIBUS and PROFINET protocols. It ensures the integrity of failsafe signals transmitted between safety devices and a safety controller, adhering to relevant safety standards. PROFIsafe functions independently of automation processes, even though it operates on the same network. It can be used with either PROFINET or PROFIBUS, individually or in combination, in various factory and process automation applications.
PROFIsafe has been available since 2001, and currently, there are over 21,7 million operational PROFIsafe devices. It is approved for wireless transmission channels such as WLAN and Bluetooth, and can even be deployed on open Industrial Ethernet backbones.
It is important to note that safety is a critical aspect of automation, and the dissemination, implementation, and deployment of PROFIsafe technology must be treated with utmost seriousness. All companies and institutions involved with PROFIsafe adhere to the PROFIsafe Policy.
PROFIsafe offers a flexible safety architecture that meets the highest safety categories, such as SIL3 according to IEC 61508/IEC 62061, Category 4 according to EN 954-1, or PL "e" according to ISO 13849-1. The PROFIsafe profile reduces error probabilities in transmitted data between F-devices and F-controllers to meet or surpass the required levels specified by relevant safety standards. The PROFIsafe protocol conducts a series of safety checks to ensure this integrity.
Importantly, PROFIsafe does not impact standard bus protocols, allowing the automation system connected to the same network to operate normally without interference. All F-devices and F-controllers undergo rigorous conformance testing to the PROFIsafe protocol by PI Test Laboratories and receive certification from PI for field usage. Additionally, safety and standard data can be transmitted over the same cable, and it is possible to mix safety and standard modules in a single station, offering a flexible and efficient solution.
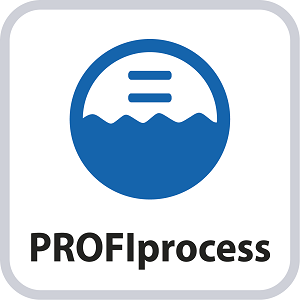
PROFIprocess provides the PROFINET solution portfolio for process automation (PA), spanning different application profiles such as PA Profile 4 and RIO for PA.
PROFINET serves as the main network backbone in process plants, but there are still areas where Industrial Ethernet is not suitable, such as hazardous environments. In these cases, PROFIBUS PA is commonly used. This is not a limitation of PROFINET itself, but rather a limitation of Ethernet, as it was not originally designed for hazardous area applications.
PROFINET offers a high-speed and high-bandwidth backbone for fieldbus networks like PROFIBUS PA. It utilizes a "proxy" interface, which acts as a bridge between PROFINET and the underlying bus. The proxy enables transparent communication, making instruments on the fieldbus appear directly connected to the PROFINET controller as remote I/O. This approach simplifies the configuration, maintenance, and management of the automation system from any part of the enterprise. Proxies are available for various bus technologies, including PROFIBUS PA, Foundation Fieldbus, and WirelessHART. The advantage of using proxies is that existing field networks do not need to be replaced when migrating to PROFINET, ensuring protection of investments in skills and inventory during the transition to Industrial Ethernet architectures.
Furthermore, the PROFINET backbone can be utilized to connect other field devices commonly found in process applications, such as drives and discrete I/O. Since most process plants are hybrid in nature, combining both process and discrete automation elements, a single network (PROFINET) can cover the entire plant.
PROFINET also supports three additional key needs in process automation:
- Configuration in Run (CiR): It allows changes to be made to an application program without stopping the controller, enabling flexibility in modifying the system during operation.
- Time Sync / Time Stamping: PROFINET provides the ability to record actions, alarms, and status messages as a sequence of events, which is essential for accurate event logging and analysis.
- Fieldbus Integration: PROFINET ensures investment protection by integrating plant units using proxies, allowing for a smooth transition and coexistence of different automation technologies.
Scalable redundancy is another requirement specific to process automation, and while PROFINET already supports media redundancy, there is a need to further support system redundancy to meet the demands of process applications.
Based on IEEE and IEC standards, Ethernet-APL supports PROFINET and any other Ethernet-based automation protocol and will develop into a single, long-term stable technology for the entire process automation community.
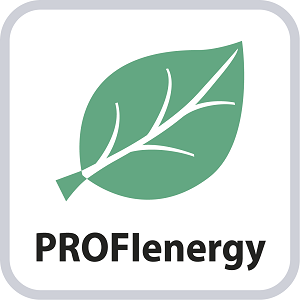
PROFIenergy introduces a novel approach to energy savings in automation systems. By leveraging PROFINET, automation controllers on a network can intelligently determine when end devices should enter sleep or OFF modes to conserve energy during various periods.
Through the establishment of a standardized open profile, PI (PROFIBUS & PROFINET International) enables collaboration between vendors and users in implementing intelligent energy management strategies using PROFIenergy.
User Benefits:
- Energy and cost savings.
- Compliance with laws and regulations related to environmental protection.
OEM Benefits:
- Ease of programming through loadable function blocks.
- Competitive advantage in the market.
Device Maker Benefits:
- Unique selling proposition and competitive edge. Builds upon the existing PROFINET protocol.
PROFINET transmits standardized PROFIenergy commands to end devices and receives status information and energy consumption data in return. PROFIenergy data utilizes the acyclic slots of the PROFINET communications protocol, ensuring that it does not interfere with normal PROFINET processes. As a result, PROFIenergy can be seamlessly integrated into existing automation architectures.
Furthermore, PROFIenergy can be utilized to balance energy demand and manage peak load conditions effectively, helping to avoid costly penalties associated with high energy consumption during peak periods.
Overall, PROFIenergy offers a powerful tool for achieving energy savings in automation systems, providing benefits to users, OEMs, and device makers alike, while leveraging the robustness and versatility of the PROFINET protocol.
The Simple Device Replacement feature in PROFINET is a unique capability within the industry that facilitates fast and effortless replacement of PROFINET devices in an automation network.
When a device fails in the network, it can be replaced with a new device without requiring any user configuration. The process is straightforward: the user manually replaces the failed device with a new one, and the controller automatically detects the presence of the new device. The controller then assigns the appropriate IP address, name, and related configuration to the replacement device. This means there is no need to use engineering tools or reconfigure the network manually.
To successfully utilize the Simple Device Replacement feature, there are three requirements:
- The replacement device must be the same model as the device it is replacing. This ensures compatibility and proper functionality within the network.
- The replacement device must have a blank name. This helps avoid conflicts with existing device names in the network.
- The controller must support the Simple Device Replacement feature. This functionality needs to be available in the specific controller being used.
However, it is important to note that users have the option to bypass the second requirement mentioned above. Some controllers provide a function that allows for name overwrite. If this option is enabled, the replacement device can have the same name as the device it is replacing, even if the name is not blank.
Overall, the Simple Device Replacement feature in PROFINET simplifies the process of replacing failed devices in an automation network by automating the configuration and eliminating the need for manual intervention and reconfiguration.
The PROFINET Fast Start Up (FSU) feature enables IO Devices to instantly transition to a "power on" state upon receiving signals from an IO Controller. This capability is particularly valuable for industrial robots with Automatic Tool Change (ATC), as it enhances the flexibility of production lines and reduces the number of robots required per cell.
In applications such as car body production, where cycle times for a single robot cell can be as low as 45 seconds (including tool change delay), the speed of start-up becomes crucial. Many Industrial Ethernets experience slow start-up times, typically in the range of seconds, compared to the faster start-up times in the 100 ms range offered by fieldbuses. This slower start-up can be inadequate for meeting the demands of fast-paced production requirements. By optimizing the PROFINET protocol and the utilization of data by end devices, significant reductions in start-up times can be achieved.
PROFINET FSU defines the time interval between "power on" and the receipt of the first cyclic input data to be less than 500 ms. The necessary protocol optimizations to achieve this are standardized within the PROFINET specification and include the following:
- Use of fixed transmission parameters (only applicable for copper wires) instead of automatic detection, resulting in a reduction of up to three seconds in start-up time.
- Network addresses are not transmitted to IO devices during every cycle but only during initial start-up. Parameters are stored in the IO device memory and reused, potentially saving several seconds.
- IO Devices proactively announce their readiness to establish communication instead of waiting for the IO Controller to search for them. This approach can save up to one second in start-up time.
From the perspective of OEMs and end-users, additional optimizations are possible. For instance, start-up time can be further reduced by employing suitable hardware. Wireless communication can also play a role in enhancing start-up speed by either maintaining continuous communication or establishing communication in advance of the actual "power on" event.
By implementing these optimizations, PROFINET FSU enables swift start-up times, improving the efficiency and responsiveness of automation systems, particularly in applications where rapid tool changes and high production rates are critical.