PROFIdrive - The Leading Drive Control Profile
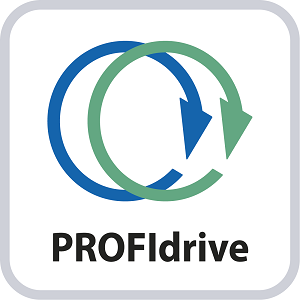
PROFIdrive is a powerful and mature drive control profile for any kind of application and industry usage.
This profile is standardized in IEC 61800-7 (Generic interface and use of profiles for power drive systems) as well as GB/T 25740 and hosted by Profibus & Profinet International (PI), which guarantees professional support around the globe.
Due to its modular structure and manufacturer-independent device profile, PROFIdrive is easy to integrate, highly scalable by its granular six-level structure, and defined to achieve the utmost interoperability level. PROFIdrive is safeguarded by well-defined certification tests, global technology support and easy implementation procedures.
Another huge advantage is the complete upper OSI layer implementation (level 5-7), which makes this profile futureproof and independent from any changes in the lower technology layers.
By its nature, PROFIdrive always comes along with perfect interplay of all other PROFINET profiles like PROFIsafe and PROFIenergy.
The supported VIK/NAMUR drive interface - according to VE34/NE122 - offers the advantage of a "device exchange without engineering interaction" based on a specifically defined and provided VIK/NAMUR GSD file. This feature underscores the general architecture and vendor independent nature of the PROFIdrive architecture and communication structure.
PI offers a wide range of options for implementation support, interoperability testing, and certification options. Further, PI invites all companies to participate in future PROFIdrive profile enhancements and on-going standardization work.
For more than a decade, PROFIdrive is the approved international IEC standardized drive interface. Please refer to IEC standard 61800-7 "Generic interface and use of profiles for power drive systems“ for additional details.
In 2013, PROFIdrive was standardized in China as GB/T 25740 national standard. Overall, PROFIdrive is recommended by various international institutions such as OMAC and VIK/NAMUR.
The supported VIK/NAMUR drive interface - according to VE34/NE122 - offers the advantage of a "device exchange without engineering interaction" based on a specifically defined and provided VIK/NAMUR GSD file.
The successful admission of PROFINET and PROFIdrive into internationally recognized standards bodies, together with the close cooperation of key institutions in the industrial sector, ensures that PROFIdrive continues on as an innovative and futureproof profile.
One of the major strengths of PROFIdrive is the optimal interoperability and exchangeability offered for all the motion control applications.
This strength also includes the safety functions, which are becoming increasingly important.
Device Profiles describe specific device properties that have been jointly specified by device manufacturers for uniform implementation into their devices.
Devices with the same device profile will - irrespective of the manufacturer - exhibit the same behavior on a bus system.
The importance of such interfaces is increasing with respect to the enormous data quantities that are being exchanged as the degree of automation advances.
PROFIdrive covers all industrial automation use cases. In industry, there is an enormous variety of drive products required to cover the complete range of applications, and consequently, there exists a very broad spectrum of Application Classes (AC) for drives. To allow the best possible implementation scaling, PROFIdrive defines up to six application classes. From simple single axis up to multi axis and high demanding drive use cases.
Based on this approach PROFIdrive allows a flexible, cost-effective, and specific market segment compliant device implementation. There is also the freedom to use certain manufacturer add-ons to differentiate with specific drive products and implement unique selling features to maximize competitive advantage.
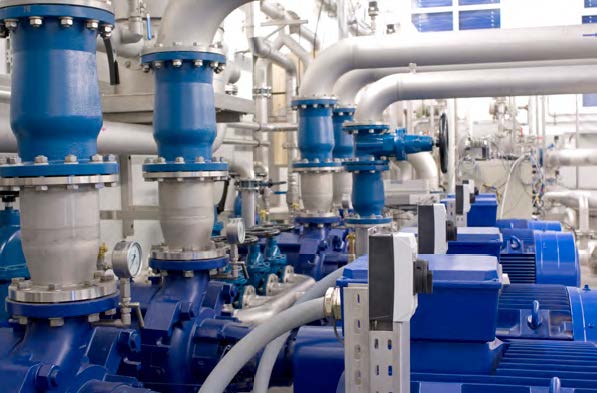
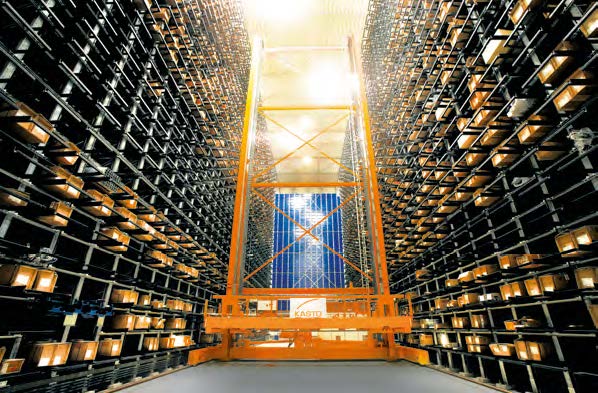
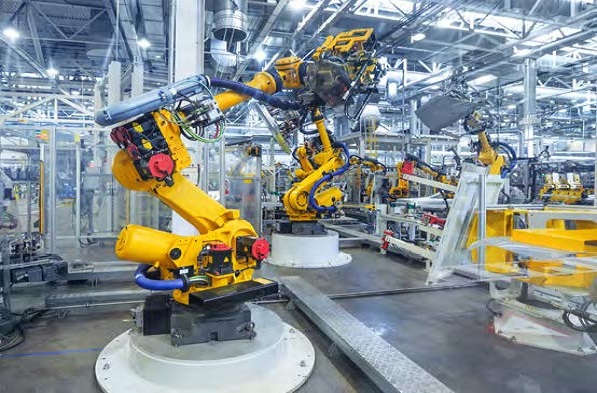
By implementing PROFIdrive at ISO/OSI layers 5-7, device features are independent from the transmission properties on layers 1-4 below.
Adaption at lower OSI layers can be established without impact on PROFIdrive, like, for instance, a later migration to Time Sensitive Network (TSN) enhancements.
This specific design approach makes PROFIdrive futureproof.
In addition to traditional drive functions such as speed, position and motion control, drives are integrating more and more additional functions that were previously implemented externally and are nowadays becoming an integral part of the drive.
Two typical examples of this are drive-based safety technology and energy management functions.
These additional drive functions require new communication relationships with additional communication profiles. Drive technology is therefore a typical example of PROFIBUS and PROFINET devices that not only support their original application profile but also other additional profiles (common application profiles).
To ensure smooth interaction between these additional functions and the basic PROFIdrive functions, definitions and specifications regarding this interaction have been included in PROFIdrive.
PROFIsafe
Integration of safety technology into the drive is beneficial because it eliminates the need for external monitoring devices, thereby reducing engineering effort, wiring expenses and space requirements.
From this point of view, the PROFIdrive and PROFIsafe profiles are the perfect complement to one another.
Together, the two profiles create a harmonious unit that enables the same bus to be used to control safety functions and standard drive functions.
PROFIenergy
Electric drives account for a large portion of industrial power demand. With continuously rising energy prices, this cost factor is driving up production costs more and more.
On the positive side: this represents an enormous savings opportunity for practically all companies. Especially in high energy-consuming areas, significant savings are possible using energy-efficient drives and intelligent energy management.
This is where PROFIenergy comes in by providing a uniform, device-/vendor-neutral interface for controlling energy saving functions in PROFINET devices.
- Regional PI Associations – provide regional support of PROFIBUS and PROFINET and localized marketing activities.
- PI Competence Centers – give high-quality technical support for developers and users of PROFIBUS and PROFINET products and systems.
- PI Training Centers – offer a high level and comprehensive training environement to engineers and users.
- PI Test Labs – provide a wide range of test and certification services to ensure highest quality and performance of PROFIBUS and PROFINET products.
The tasks performed by drives, and thus the requirements for the drive technology, vary considerably depending on the specific industry and/or field of application.
These include:
• Drives with fixed and variable speed, such as pumps, fans, compressors, and drives for transport tasks
• Single-axis positioning controllers for applications, such as moving, adjusting and positioning
• Servo drives with central interpolation, such as those found in machine tools, robots and production machines
With such a diverse range of requirements, a technology that is flexible as well as adaptable to future requirements is needed to serve as the basis for efficient implementation of products.
As a general principle, drives can be controlled very easily using the digital drive interface with all its functions. For a single drive in such a communication link, it does not matter how this communication link is modeled.
Existing products can be upgraded by simply transferring the device and communication models already in the drive to PROFIBUS and PROFINET. But products can only be replaced with products of the same manufacturer or the same product family.
For a drive user, it is also important to be able to select from drives made by various manufacturers having an identical communication interface to use the optimal product for the particular application.
This is only possible with a standardized drive interface such as PROFIdrive for PROFIBUS and PROFINET.
This application-oriented profile, which has been standardized in IEC 61800-7, contains standard definitions (syntax and semantics) for communication between drives and automation systems for PROFIBUS and PROFINET, thus assuring vendor neutrality, interoperability, and investment protection.
The PROFIdrive application profile represents a flexible and futureproof foundation for all drive systems in industrial automation engineering. It defines the device behavior and the process for accessing drive data of electric drives on PROFIBUS and PROFINET and optimally integrates the additional PROFIsafe and PROFIenergy profiles
PROFIdrive is the standard profile for drive technology in conjunction with the PROFIBUS and PROFINET communication systems. The use of open "application profiles" is a tried-and-tested way of using communication systems to connect drives and controllers from different manufacturers in an interoperable
and straightforward way.
The PROFIdrive profile has been specified by a working group made up of numerous device manufacturers under the PI (PROFIBUS & PROFINET International) umbrella. This working group is also responsible for continuous updates and enhancements.
Work on PROFIdrive can be traced back to 1991 when the focus was on PROFIBUS DP. The widely used profile version 2.0 appeared in 1997. In 2002, profile version 3.1 introduced the synchronous servo interface based on PROFIBUS DP-V2. In 2005, V4.0 saw the inclusion of PROFINET as a further communication system (supported by the version number 4).
Also in 2005, the PROFIdrive on PROFIsafe Amendement was released, which now includes the Drive Based Safety functions from PROFIdrive. The PROFIdrive interface has been continuously developed and enhanced with new features ever since.
The basic and specifications in the PROFIdrive standard are the following:
- Base Model: All these functions are independent of the underlaying communication system.
- Parameter Model: This is valid for basic fieldbus up to a system-wide Ethernet network with identical application view.
- Application Model: Drive technology can be linked without exception and without changes to the automation application.
The PROFIdrive base model defines a general drive application as a set of devices with associated communication relationships (cyclic and acyclic data exchange), irrespective of the communication system used.
The following device classes are included:
1. Supervisor → e.g. Engineering Station or HMI
2. Controller → Controller or host automation system, e.g. PLC, NC or RC
3. Peripheral device (P device) → Drive device with 1 to N axes - each axis is an own drive object (DO)
Cyclic data exchange
During operation of a drive application, the open-loop and closed-loop control processes must be activated cyclically.
From the point of view of the communication system, this means that new setpoints must be transferred cyclically from the control application processes to the drives and current actual values also must be sent in the opposite direction.
The cyclical transfer can be carried out both isochronously as well as non-isochronously, depending on the requirements of the application and the selected PROFIdrive application class.
For typical drive applications in application classes 4, 5, and 6, the jitter of the clock signal must be guaranteed to be less or equal than 1 µs.
Alarm mechanism
The alarm mechanism is event-controlled and is used to signal the setting and clearing of maintenance or fault conditions of the drive axis and/or device.
Acyclic data exchange
In addition to the cyclic setpoints and actual values, parameters are used for parameterizing the application processes. The controller accesses these parameters acyclically since this access is not time-critical.
The parameters can be accessed not only by the controller but also in parallel by a supervisor (commissioning, operator, maintenance station)
Isochronous operation
Any modern drive profile must be able to support isochronous operation of distributed drives of a drive application, because this is the only way of accurately coordinating the movements of several axes (such as path traversing in NC/RC systems or synchronizing movements associated with electronic gears).
This means that a drive profile must fulfill two basic requirements:
- Synchronization of multiple application processes on different devices to a common master clock
- Assurance that cyclic data exchange between processes is completed reliably within a defined point in time so that all relevant input and output data are available on-time for further processing
For process synchronization, PROFIdrive makes use of device clocks that are located in every device and are precisely synchronized with the system's master clock (Figure 2).
For synchronization of the device clocks, PROFIdrive utilizes the appropriate services of the particular communication system. For PROFIBUS, this functionality is an integral component of DP-V2.
For PROFINET, it is a component of the isochronous real-time functionality (PROFINET IRT). Here, it is not just the frame traffic on the bus system that is realized in an equidistant time base, but also the internal control loop algorithms including speed and current control in the drive or control of higher-level automation system, for example.
Typical drive applications in application classes 4, 5, and 6, the jitter of the clock signal must be guaranteed to be less or equal than 1 µs.
Device-to-device communication
Device-to-device communication enables direct data exchange between devices without having to transfer data using master/controller. As a result, it is possible for drives to receive actual values from other drives with minimum delay. This enables the simple implementation of high-performance, cross-axis control loops.
This opens new fields of application, especially in distributed drive applications. An example of this is the transfer of speed setpoints for the purpose of creating a setpoint cascade for paper-, film-, wire-, and fiber-drawing machines.
While device-to-device communication still plays a major role in motion applications with PROFIBUS, it is no longer used in modern motion applications with PROFINET.
The reason for this is the significantly increased performance of PROFINET which led to the establishment of central PLC-based motion control concepts that are remarkably more convenient to engineer.
Operating modes and basic state machine
A uniform basic state machine is defined for all application classes in PROFIdrive. It is used to bring the drive to a dedicated operating state or switch off the drive in a defined manner.
For application class 3 "Positioning drive", the basic state machine is extended to include the positioning state machines for controlling the positioning function.
The figure below shows the basic state machine (general state diagram) of a PROFIdrive drive. The blue blocks represent drive axis states S1 to S5 and the arrows indicate the state transitions that are possible between them. In the case of competing state transitions, priorities are defined by the number of red points shown. The conditions for the state transitions to the yellow boxes are the individual control commands, which are transferred from the controller to the drive axis in the control word with bit coding.
Frames
In cyclic data frames, the control word and the status word form the command interface for the control of the basic state machine by the controller. Individual bits of the control and status word are assigned according to the respective application class.
In addition to the control and status words, the setpoint and actual values of the drive axis are transferred via the cyclic interface.
PROFIdrive describes the cyclic data interface as a string of signals. In this regard, PROFIdrive signals are control and status words as well as setpoints and actual values. The signal number serves to uniquely define the content of a signal as well as its transfer format.
For simplification purposes, typical cyclic interface implementations of PROFIdrive are defined as PROFIdrive frames. Thus, a PROFIdrive frame number signifies a permanently defined grouping of PROFIdrive signals that uniquely describe the cyclic interface.
The PROFIdrive frames are fundamentally identical for both PROFIBUS and PROFINET. A manufacturer can also use additional vendor-specific frames and signals for a specific application case.
Parameter manager
The PROFIdrive parameter manager, which is operated via the acyclic communication channel, provides users with comprehensive services for accessing the PROFIdrive parameters.
In addition to reading and writing parameter values, additional parameter attributes, such as a parameter description, can also be used. To improve performance in the acyclic parameter channel, a multi-parameter service is also defined for the parameter manager.
PROFIdrive defines a drive model that can be found today in nearly every drive system. The device comprises various function modules that represent the intelligence of the drive system. These function modules are assigned parameters, which are used to configure and parameterize the function module. In addition, parameters are also used for internal representation of input and output values of the function module ("Setpoint values", "Actual values"). The function module can be integrated in the cyclic data exchange by interconnecting parameters to the cyclic interface ("Telegrams") accordingly.
The PROFIdrive parameter object has, in addition to the parameter value, additional properties such as the parameter description and the parameter text.
This allows Clients to browse generically through the parameter database and read out all parameter properties from the drive that are relevant for the Client (e.g. physical unit, data type, high/low limit value).
The PROFIdrive parameter channel therefore is the basis for the wide range of non-real time-critical tasks in a drive application, such as:
- Parameter assignment and commissioning
- Data backup for device replacement
- Extended diagnostics, such as trace and diagnostics buffer
Profile-specific parameters
The PROFIdrive profile uses parameter numbers from 900 to 999 and from 60,000 to define parameters uniformly for all drives, independent of the application classes. These parameters are designated as profile-specific parameters and ensure interoperability and generic identification of the drive and drive interface. For example, functions for drive identification, fault buffer, drive control, device identification, frame configuration, and the complete list of implemented parameters are available via profile-specific parameters.
Vendor-specific parameters
Besides the parameters described in the profile, manufacturer-specific parameters can also be used and be differentiated depending on the manufacturer, drive and supported drive functionality.
Drive manufacturers can benefit from the advantages of a drive profile without having to forego innovations and unique selling features that provide a competitive edge.
A drive application consists of:
- application processes in the drive, typically motor current control and speed control, as well as
- application processes in the controller, which may include things like simple speed setpoint
setting, position control, or path interpolation, and - a communication system, which provides the relevant services for data exchange and, if necessary,
for synchronization between the application processes.
Application classes
The way drives are integrated into automation systems is heavily dependent on the drive application.
There is an extremely broad range of drive applications depending on the market segment and device implementation.
Therefore, there are six application classes defined to accommodate the different drive types. PROFIdrive application classes allow a flexible, manufacturer-specific design of drive products to meet particular market requirements.
Depending on the market segment and the type of unit, a drive can cover one or more application classes.
Single Axis Positioning Drive with local position control and trajectory generator
In this class, the drive features positioning control in addition to the drive control (speed and position control). The drive thus acts as an autonomous single-axis positioning drive, while the higher-level technological processes run on the controller.
Positioning tasks are transferred to and started on the single-axis positioner and drive via PROFIBUS DP or PROFINET IO. Positioning drives have a very wide range of applications as seen in positioning drives or in more simple motion applications without path reference.
Multi axis contouring with centralized trajectory generator and position closed loop control
Central motion control application class 4 & 5 defines an interface between the speed setpoint interface and actual position value interface, where speed control is executed on the drive and position control on the controller, as it is typically required in robot and machine tool applications.
Multi axes motion control is performed centrally, for example, by numerical control (NC) and the position control loop is closed by means of the bus. Clock synchronization is required to synchronize the clocks for the position control in the controller and for the speed control in the drives (PROFIBUS DP-V2 or PROFINET IRT).
Distributed drive-based motion control
For decentralized isochronous communication and clocked automation like electronic shafts, where the controller (PLC) is not involved in the axis coupling. Typical applications are angle-synchronous operation, such as “electric gear”, “cam disk” or “flying saw”.
PROFIdrive application class 6 has often been used with PROFIBUS to save resources on the PLC. The AC6 is no longer used in today's systems and axis couplings in PROFINET are implemented by corresponding technology objects on the PLC.
Figure 4 shows the range of drive diagnostic functions available with PROFIdrive. These are generally organized into mechanisms for handling warnings and for handling faults.
This two-level concept enables emerging problems to be signaled at an early stage so that preventive actions can be taken in time. Drives can thus be easily incorporated into a plant-wide maintenance concept.
Warnings
Warnings are a form of message that is acknowledged automatically as soon as the cause has been addressed. They provide advance warning so that appropriate measures can be taken in good time for the purpose of preventing a fault condition.
Several warnings can exist at the same time (e.g., "elevated motor winding temperature" and "DC link voltage too low"). Unlike errors, warnings do not cause the drive to stop. The profile defines parameters for the warning mechanism, each of which represents a so-called warning word. Each warning that occurs within a drive or drive axis is mapped to one bit of the warning word.
Faults
A fault condition in the drive (e.g., overtemperature) always triggers a device-specific response, i.e., the drive will generally be shut down. At the same time, one or more fault messages describing the fault condition will be entered in the fault buffer (Figure 4).
A fault entry in the PROFIdrive fault buffer consists of the device-specific fault number, an optional application-specific fault code, and an optional associated value or fault time (Figure 5). The device-specific fault number and fault code information enables very detailed device-specific diagnostics.
Whenever the cause of a fault is eliminated, the user must always explicitly acknowledge the fault by means of a command. The acknowledged fault is not deleted but rather archived in the fault buffer, which allows subsequent tracking of faults. The size of the fault buffer can be specified on a device-specific basis.
Integration into standard diagnostic mechanisms
For cross-vendor diagnostics, PROFIdrive provides a simplified profile-specific diagnostics view of PROFIdrive fault classes (Figure 5, "Fault classes mechanism") in addition to the detailed diagnostics view of fault buffers and warning words.
With the help of the PROFIdrive fault classes, it is possible to achieve a uniform and consistent diagnostics view for all PROFIdrive drives, in which fault classes are structured according to typical modules and function blocks of a drive and which supports users and service personnel in carrying out fast, systematic troubleshooting.
These warnings and faults are signaled as alarm objects (fault, maintenance demanded, maintenance required) to the higher-level controller via the standard PROFINET alarm channel.
The profile defines parameters for the warning mechanism, each of which represents a so-called warning word. Each warning that occurs within a drive or drive axis is mapped to one bit of the warning word.
This ensures consistent integration of the PROFIdrive drive into the standard diagnostics system of PROFIBUS and PROFINET.
Summary: Relation between application classes, basic and interface functions
The following graphic provides an overview about the relationship between most common application classes, basic and interface functions basic interface functions. It shows the modular structure of PROFIdrive and the resulting scaling advantages. The standard basic functions are required as a basic framework for the implementation; beyond this it is only added what is necessary for the respective application class.
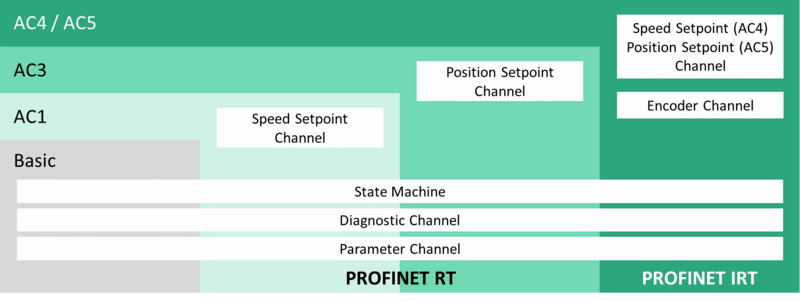
All the implementation stages of the PROFIdrive profile shown here can be realized as pure software implementation tasks. And tried-and-tested software modules are available for all of them as part of the community project. Specific hardware on the underlying PROFINET connection is only required for high-end applications where isochronous task synchronization is absolutely essential. But even if this PROFINET IRT functionality is required, various well-established solutions from the PI community can be offered.
In addition to traditional drive functions such as speed, position, and motion control, drives are integrating more and more additional functions, which were previously implemented externally but are now included in the drive.
Two typical examples of this are drive-based safety technology and energy management functions.
These additional drive functions require new communication relationships with additional communication profiles. Drive technology is therefore a typical example of PROFIBUS and PROFINET devices that not only support their original application profile but also other additional profiles (common application profiles). To ensure smooth interaction between these additional functions and the basic PROFIdrive functions, definitions and specifications regarding this interaction have been included in PROFIdrive.
PROFIsafe
Integration of safety technology into the drive is beneficial because it eliminates the need for external monitoring devices, thereby reducing wiring expenses and space requirements. From this point of view, the PROFIdrive and PROFIsafe profiles are the perfect complement to one another. Together, the two profiles create a harmonious unit that enables the same bus to be used to control safety functions and standard drive functions (Figure 6).
The safety functions on the drive are controlled by means of cyclic frame exchange with a higher-level safety user program via a safe PROFIsafe transmission channel. For purposes of efficient operation, it is very important to coordinate the sequences on the Safety Controller with those on the drive control. Thus, for example, preliminary measures such as speed reduction or motion restrictions must be taken on the motion control drive before selecting safety functions, which explains why the drive control requires direct information exchange with the Safety Controller and with the safety process on the drive (additional safety information). In this case, PROFIdrive defines standardized flexible extensions for standard frames that can be used in all application classes.
The shared-device concept of PROFINET enables standard and safety functions to be distributed among different physical controllers/PLCs, thereby significantly expanding the usability of integrated safety technology.
The PROFIdrive profile supports the Drive Based Safety functions STO, SS1, SS2, SOS, SLA, SDI, SLS, SLP, SS, SP and SCAM in the PROFIdrive on PROFIsafe amendment.
PROFIenergy
Electric drives account for a large portion of industrial power demand. With continuously rising energy prices, this cost factor is driving up production costs more and more. On the positive side: this represents an enormous savings opportunity for practically all companies. Especially in high energy-consuming areas, significant savings are possible through the use of energy-efficient drives and intelligent energy management. This is where PROFIenergy comes in by providing a uniform, device-/vendor-neutral interface for controlling energy saving functions in PROFINET devices.
Consumption analysis
For the consumption analysis, it is necessary to systematically measure the energy flows in the plant using a higher-level energy management system. Modern drive technology is equipped with sensors for current and speed control and, thus, performance data measurements already exist. So far, however, this data has not been made available at all or only on a manufacturer-specific basis. Standardization of the energy information functions in PROFIenergy means that the drive can be easily integrated into the consumption analysis, thereby eliminating the need for additional costly energy measuring devices. In addition, the performance and energy measurements for the drive can also be used for process and plant diagnostics.
Standby management
The standby management function of PROFIenergy can be used to place the idle PROFIdrive drive in an energy-optimized standby state. In so doing, PROFIenergy communicates the expected idle time duration to the drive. The drive can shut down subprocesses or subcomponents as appropriate based on the idle time duration. To activate standby state, the drive must be deactivated by its application. That is, before a drive is placed in standby state, it must first be switched to S2 mode by its drive control.
The PROFIdrive Community has founded the working group "PROFIdrive Community Project", with the aim of providing drive manufacturers with the best possible support in implementing their own PROFIdrive architecture.
The offering of the Community Project heavily reduces the effort for the implementation and avoiding typical pitfalls during development process by providing all members with tried and tested software and hardware components as well as proven implementation guidelines.
A further big benefit is the provision of a PROFIdrive profile test equipment which supports device manufacturers during the development process and at preliminary testing phase. This powerful tool is a further major cornerstone to achieve a fast, efficient, and systematic implementation of the PROFIdrive profile into own products.
Here is an overview of various beneficial services available through the Community Project and PI Organization:
Implementation Guide
The PROFIdrive Application Guide is a valuable planning and implementation aid. It lists all the sub-functions to be
realized in detail for each application class and provides valuable tips on implementation and realization.
Reference implementation
This offer includes a license-free source code, proven in the field and usable on various platforms and operating systems. This community source code for AC1 and AC4 application classes enables the implementation of the PROFIdrive profile for controllers, drive devices and encoders on various platforms and PROFINET stacks free of charge.
FAQ + version overview report
Over many years, a PROFIdrive FAQ document has been developed to provide quick answers to frequently asked questions. These also refer to special features of individual software versions, provide a version overview and much more.
Free supporting document download
Comprising software; overviews, manuals; etc.
Provision of PROFIdrive and PROFINET profile test equipment
This powerful und very useful toolset enables fast, efficient, and systematic implementation of the PROFIdrive profile into own products
Support from various PROFIdrive Community companies
The PI user community consists of many companies with a wide range of services, which are also exchanged and utilized within the community.
Support from PI Competence Centers
PI Competence Centers (PICCs) are centers of technical expertise and work closely together with the Regional PI Associations. There are currently 59 PICCs, a virtual guarantee of global support wherever interested companies happen to be located.
PICCs offer technical support to anyone who needs it and they play an essential role in supporting first-time developers of PROFIBUS and PROFINET devices and systems. PICCs often support local RPAs in the delivery of technical seminars and workshops.
PICCs can also act independently to provide a non-partisan service respecting commercial sensitivities all the while bringing the synergy of the global organization to bear on the development of PROFIBUS and PROFINET products.
PICCs are governed by 'Quality of Services' Agreements administered by PI to ensure the technical excellence of the service they deliver.
Support from PI Training Centers
Approximately 30 PI Training Centers (PITC) have been set up with the aim of establishing a global training standard for engineers and technicians. The accreditation of the Training Centers and the experts that are based there ensures the quality of the training and, thus, the quality of the engineering and installation services for PROFIBUS and PROFINET.
Information about the PROFIdrive Community Project can be found at:
https://hilscher.atlassian.net/wiki/spaces/PROFIDRIVE/overview
Latest version of PROFIdrive Implementation guide can be found here:
https://hilscher.atlassian.net/wiki/spaces/PROFIDRIVE/pages/119374925/PROFIdrive+Implementation+Guide
Reference Implementation:
https://hilscher.atlassian.net/wiki/spaces/PROFIDRIVE/pages/119374947/PROFIdrive+Device+1
https://hilscher.atlassian.net/wiki/spaces/PROFIDRIVE/pages/119374991/PROFIdrive+Device+2
Link to free supporting document download area:
https://www.profibus.com/download
Support from various PROFIdrive Community companies
https://www.profibus.com/index.php?eID=dumpFile&t=f&f=71301&token=6c796278f149a7a28a9c393367386bffa8707805
A list of the current PICCs (Competence) can be found here:
https://www.profibus.com/aboutus/institutions-support/competence-centers
A list of the current PITCs (Training Centers) can be found here:
https://www.profibus.com/pi-organization/institutions-support/training-centers
PI mission is to push established communication technology further in terms of further enhancements of standards. And second to enable and ensure technological exchange within the community by suitable offerings for community members in the way that we all become stronger together.
The first cornerstone of a successful and reliable implementation is to have a trustful and proven ecosystem to operate on. PI provides exactly such an ecosystem with its complete support and tool offering landscape.
Finally, PI certification ensures that the devices of different manufacturers with different functional scopes conform in detail to all profile specifications. The PROFIdrive certificate is based on a well-established PROFIdrive Profile Tester every PI member can use and benefit from during entire implementation phase.
- Certification is an essential and important part of a product's quality assurance.
- Successful certification enables a trouble-free usage in any environment.
- Certified products therefore benefit from reduced installation, maintenance and support efforts.
- Most of the of the customers and users anyway require a certificate from the device vendor.
- Implemented certification significantly reduces a company's product life cycle costs.
The certification test depends of course on the technology which shall be certified. PI offers certification test for all relevant communication protocols and profiles.
With PROFIdrive and PROFINET profile test equipment and of course during PI test lab (PITL) certification process typically test cases are examined:
- hardware interface,
- all mandatory and optional functionality,
- GSD-file,
- reaction on faulty behavior,
- robustness against net load,
- proper working in a reference automation plant in a test laboratory,
- state machines.
PI supports 10 autorized PI test labs (PITL) worldwide, which assist in the certification of products with a PROFIBUS/PROFINET interface. As institutions of the PI, they are independent service providers and adhere to the mutually agreed regulations.
The testing services provided by the PITLs are regularly audited in accordance with a strict accreditation process to ensure that they meet the necessary quality requirements. A list of the current PITL locations can be found on the website.
Certification plays an important role in quality control and delivers peace of mind for end users. It ensures conformance with Standards, ensures therefore freedom of choice of supply and it underpins operational performance and interoperability.
All these benefits make it meaningful that certification for PROFINET products is mandatory.
PI Worldwide Testlabs:
https://www.profibus.com/pi-organization/institutions-support/test-labs/
Certification office:
https://www.profibus.com/products/certification-office/
FAQs about Product Certification:
https://www.profibus.com/products/product-certification
PROFINET Certification:
https://www.profinet.com/profinet-explained/certification
PROFINET Community Forum:
https://forum.profinet.com